20 things you never knew about Canon lenses
We were lucky enough to go on a tour of Canon’s amazing Utsunomiya lens factory in Japan – and this is what we learned
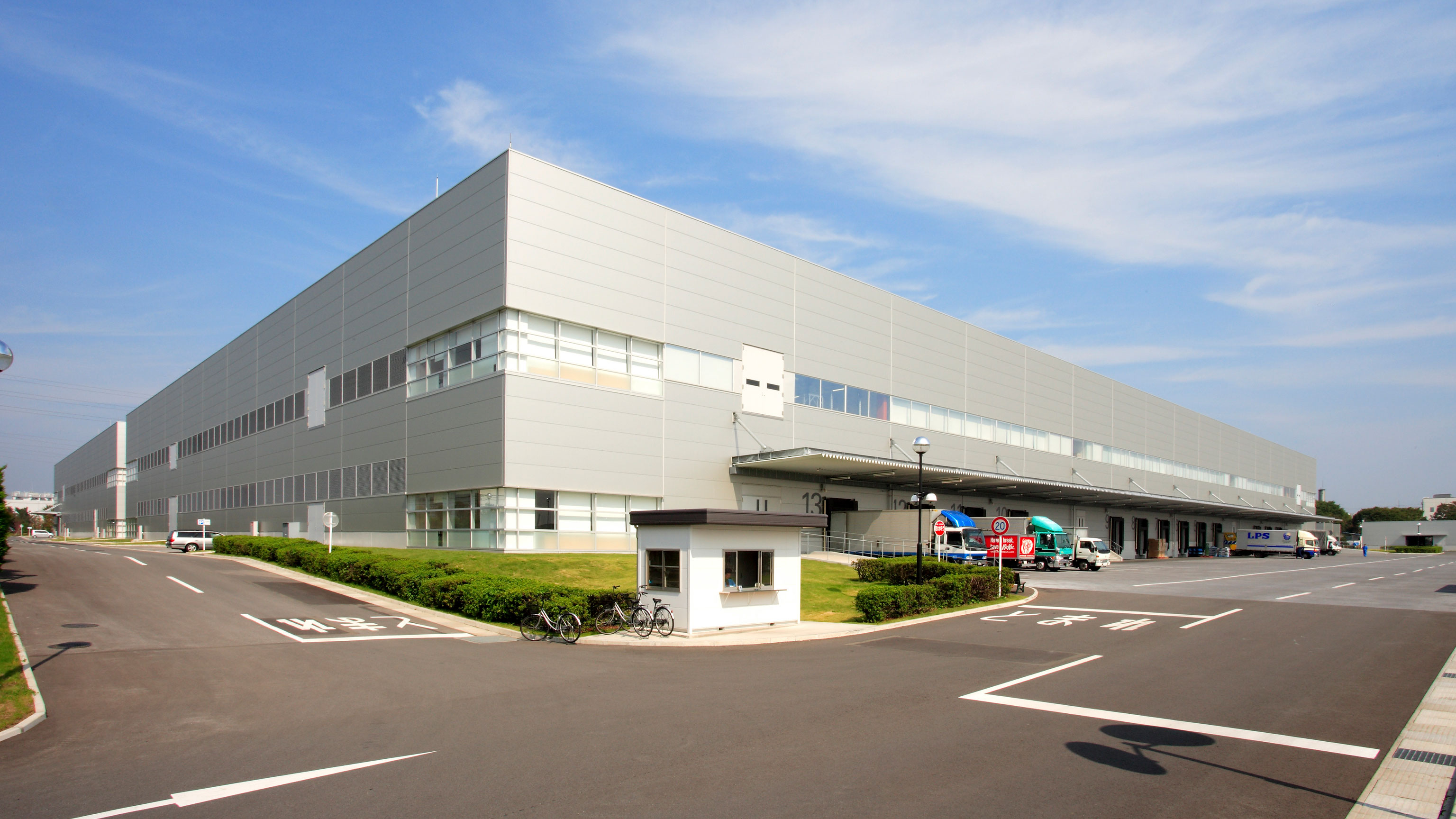
1. Canon Utsunomiya factory facts
Canon's Utsunomiya lens factory is around 60 miles north of Tokyo, and around 50 minutes by bullet train.
Spotlessly maintained inside and out, this is where Canon makes its L-series lenses using a combination of manual and automated assembly. Workers (and visitors) wear protective clothing and must pass through an air shower before entering dust-free environments.
Lens manufacturing is so precise that the plant's internal temperature must be regulated to within half a degree centigrade.
2. Lenses are designed with CAD
Lenses are designed using computer aided design (CAD) software that can take into account the physical and optical properties of the glasses being used and can predict the final lens's performance to a high degree of accuracy, and even the sample variation between lenses.
3. Why glass is great for lenses
Glass is (literally) hard to work with, but it's still the best material for making lenses. This is because it's transparent to visible light wavelengths and relatively easy to shape, and it's thermally and chemically stable – but its properties mean you can't just mould it into the shape you want.
Each glass element in a lens must be ground, smoothed and polished to the precise profile required. Typically, this is a six-stage process, including:
- Grinding the glass blank, to remove excess thickness
- Smoothing, to reduce cracks
- Centering, or grinding the lens edges to make sure it's optically centred
- Rough polishing, to reduce tiny surface cracks still further
- Fine polishing, for final shaping
- Final polishing, for fine-tuning the surface
Only at this point is the lens ready for inspection.
The best camera deals, reviews, product advice, and unmissable photography news, direct to your inbox!
4. There's more than one type of glass!
Glass is made of metal oxides and other materials arranged in an irregular pattern. Material with a regular particle arrangement is called crystal. Material that's somewhere in between is called amorphous.
The metal oxides in glass can include silicon dioxide (silicon is a 'metalloid'), calcium oxide (technically, calcium is indeed a metal), lead oxide and titanium dioxide. Every glass has different properties and advantages which the lens designer needs to take into account and utilise.
5. Dispersion, and how to deal with it
All glass produces a prism effect when light passes through it, and optical designers call this dispersion.
Different glass materials produce different levels of dispersion, and this is measured using the so-called Abbe number. (Ernst Abbe (1840-1905) was a prominent German physicist and optical scientist and one-time co-owner of ZEISS and is considered a pioneer of modern optical science).
This dispersion effect causes different wavelengths of light (which correspond with different colours) to come to a focus at different points, causing softening and colour fringing, so a lot of lens design effort goes into correcting chromatic aberration by using one lens element to counteract the dispersion of another. It's why expensive 'low-dispersion' lens elements are a key selling point for premium lenses.
6. Spherical vs aspherical lenses
Most of the lens elements in a camera lens are spherical, which means that their shape follows the curvature of a sphere. It might be a very big sphere for a relatively flat lens element, or a small sphere for a strongly curved one, but it's a sphere nonetheless.
Sometimes, though, the optical design calls for a more complex non-spherical lens element. So-called aspherical lenses are extremely difficult and expensive to manufacture using traditional grinding and polishing techniques, but Canon has its own glass-moulding machinery at its Utsunomiya plant to make them from molten glass billets.
The mould has to be designed with an extremely high level of precision, and must take into account the exact changes in dimensions that will take place as the glass cools down.
7. Mr Saito the Takumi, or 'craftsman'
As you'd expect, most of the lens processing is done by automated machinery, but at the heart of the process is the Takumi, or expert craftsman, who takes the lens design from the drawing board and helps create the physical product.
Canon's Takumi, Mr Saito, has experience, skills and even senses that the automated machinery can't yet match. "When the lens is touching the diamond plate I know what sound it should be making, so when it’s slightly off I’ll be able to detect with my hearing," he explains.
Mr Saito doesn't just make lenses by hand, he uses his experience to train the automated machinery to reproduce the tolerances and accuracy required by the designers. Mr Saito is the only Takumi at the Utsunomiya plant and he retires in four years, but he is helping to train his replacement (phew).
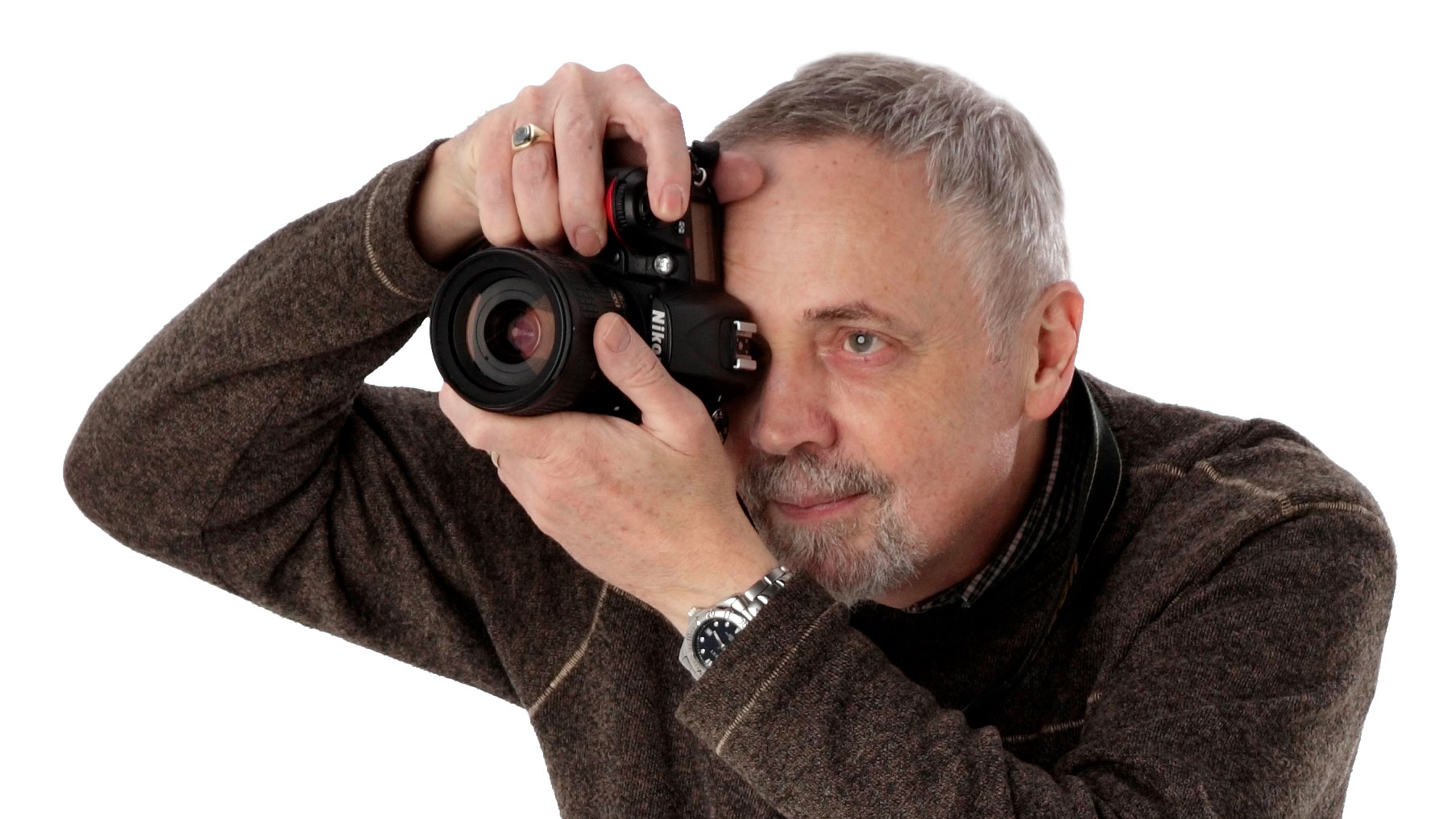
Rod is an independent photography journalist and editor, and a long-standing Digital Camera World contributor, having previously worked as DCW's Group Reviews editor. Before that he has been technique editor on N-Photo, Head of Testing for the photography division and Camera Channel editor on TechRadar, as well as contributing to many other publications. He has been writing about photography technique, photo editing and digital cameras since they first appeared, and before that began his career writing about film photography. He has used and reviewed practically every interchangeable lens camera launched in the past 20 years, from entry-level DSLRs to medium format cameras, together with lenses, tripods, gimbals, light meters, camera bags and more. Rod has his own camera gear blog at fotovolo.com but also writes about photo-editing applications and techniques at lifeafterphotoshop.com